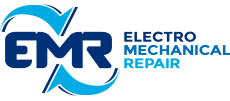
Our story begins on the 10th of October, 1988, when Ted and Paul Faint first opened their doors as Statewide Motor Rewind Company Pty Ltd. In the decades to follow, the business grew from a small, father and son endeavour to become Electro Mechanical Repair WA, an industry-leading, ISO 9001-accredited company. Over 33 years of operation and sustained growth, EMR has established itself as a respected leader in the refurbishment, rewind, overhaul and sale of a wide variety of rotating and fixed electrical equipment.
Our facility uses the most advanced tools and technology available, operated by a team of experienced, trade-qualified professionals.
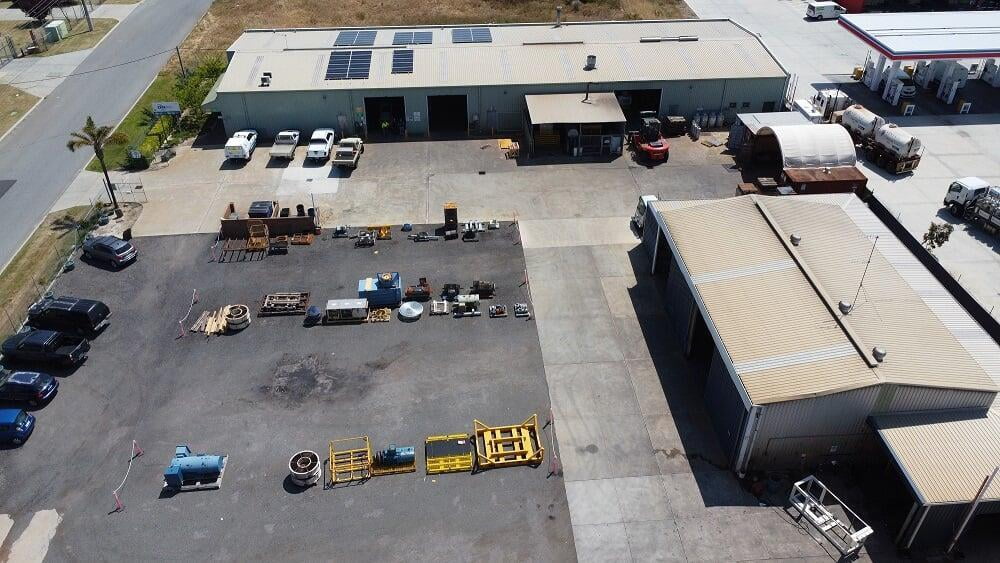
Custom Slip Ring Design
WEG were asked by a major Iron Ore producer to manufacture custom slip ring motors to drive a pair of new design side by side primary crushers. WEG’s answer are these two pigeon pair motors with opposite mounted terminal boxes. Whats a little different about these motors is they have a covered round heat exchanger which will protect the heat exchanger tubes from being blocked with fine product during operation. Also a drive end mounted slip-ring assembly which is unusual but makes perfect sense when you consider the extreme duty of these motors.
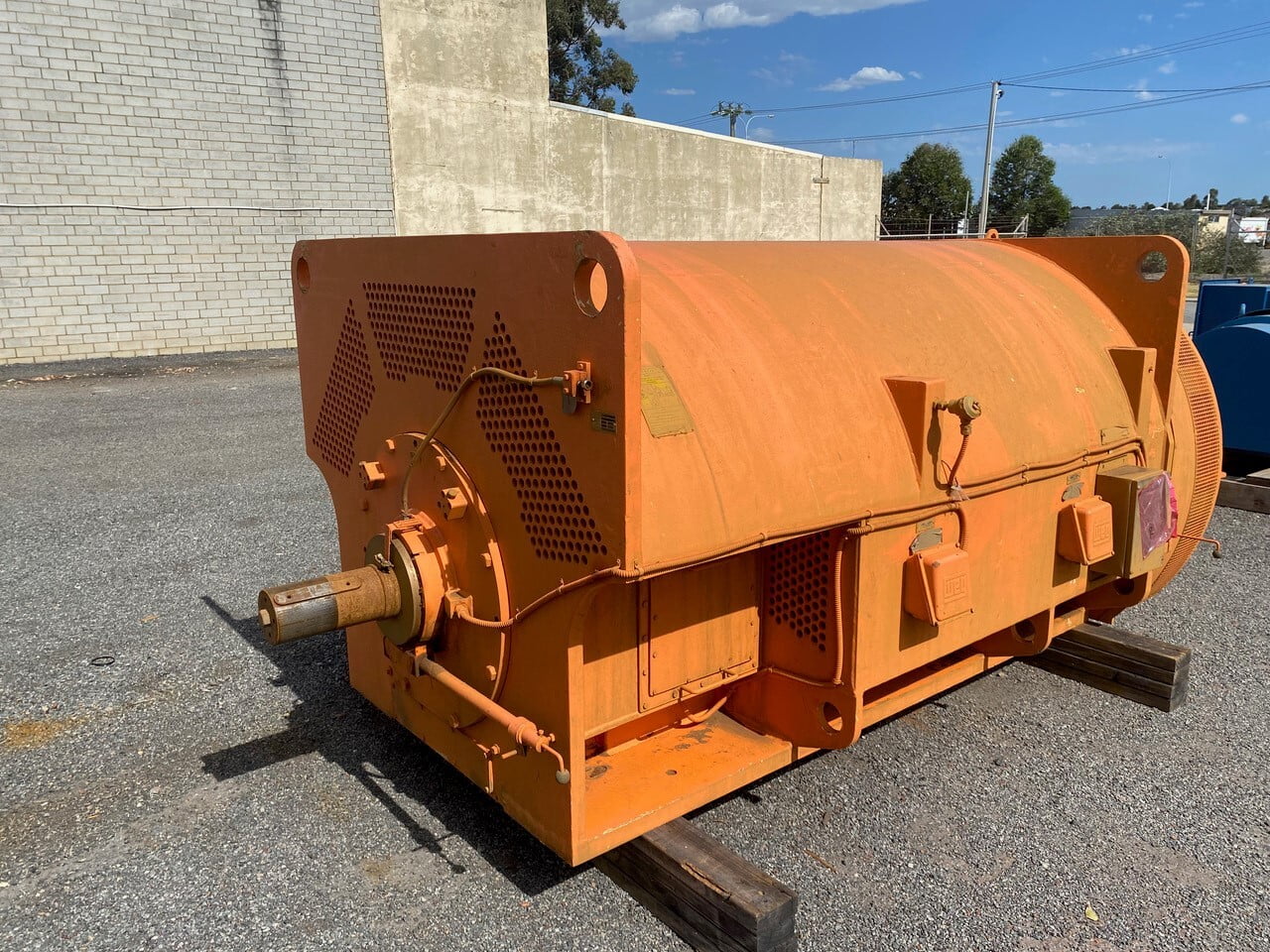

Unfortunately during the initial period of operation the motor terminal boxes were literally shaken free from their mounts. We attended site and modified the mounting arrangement calling on our experience from other similar design faults during this type of extreme violent vibration from the crushers during operation. Here is the stainless steel slip-rings being machined in one of our lathes to a acceptable finish and less than 0.001” of T.I.R (total indicated runout from the bearing journals).
The subsequent rotable spare replacement motors were modified in the factory and with a pre delivery check and final adjustments in house they have been working perfectly on site for the last 12 months. This photo shows the dynamic balancing of the whole rotor assembly to grade G1.0 which is required for final acceptance testing prior to the Iron Ore miner receiving the finished motor along with a bearing baseline test which is very important for machine reliability.
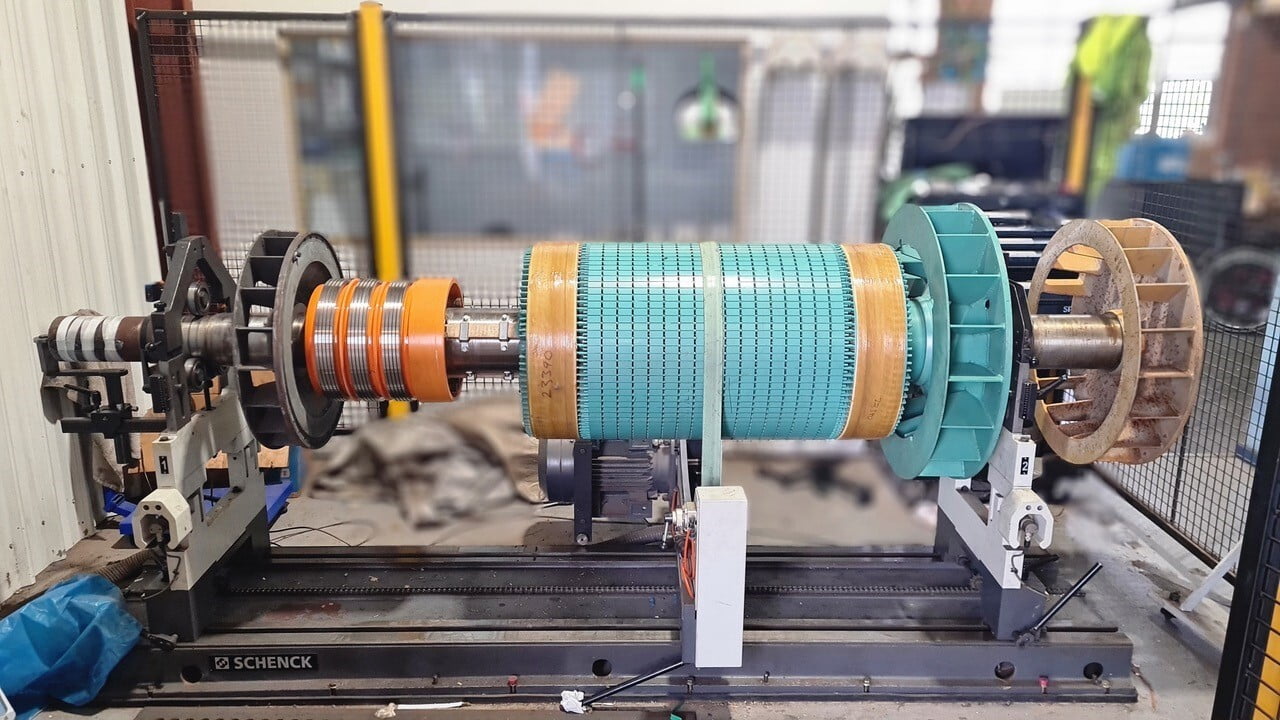
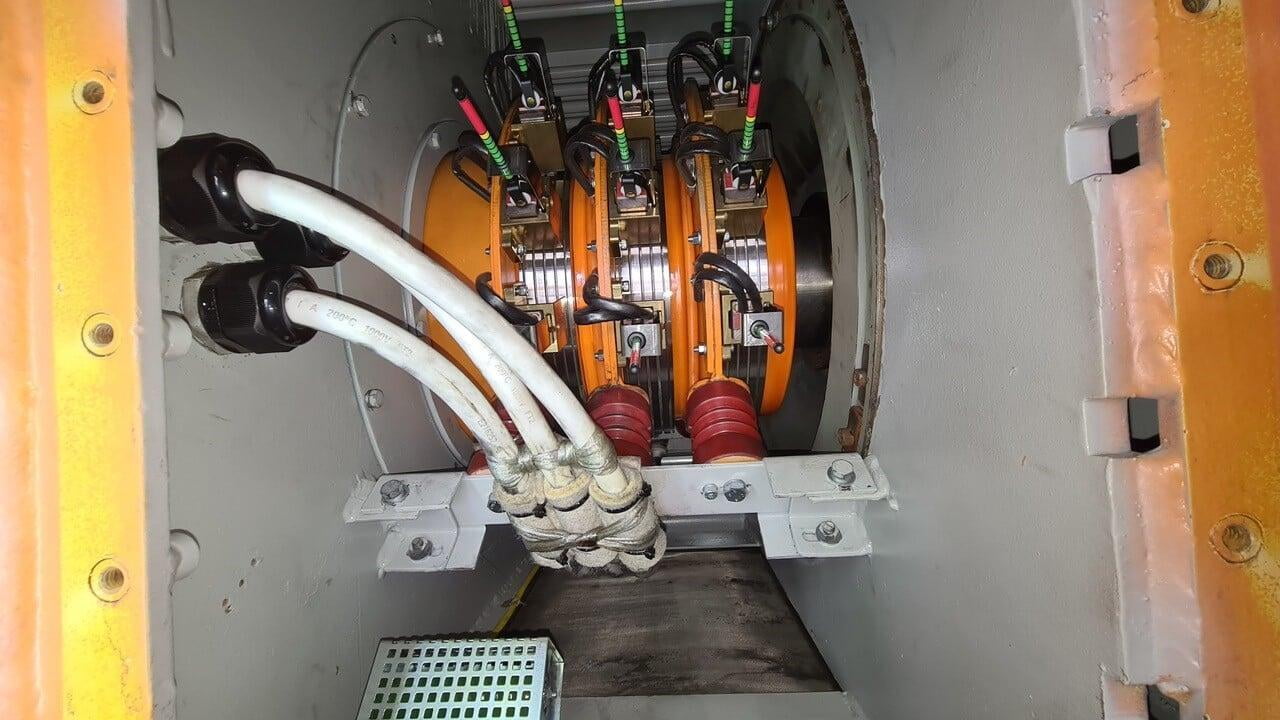
These two original motors have been modified as the factory modifications and are expected to be held in storage on site until being called for duty during a planned maintenance shut whereby the two motors taken out will be returned to us for appraisal and reporting back to the factory for continuous improvements. Here we see setting the brush boxes and bedding the carbon brushes. This is a critical aspect as these motors need to be ready for immediate full load during commissioning.
The two motors after final checks and painting with two pack recoatable urethane paint. Being able to work closely with WEG as an authorised Service Agent gives the end user the best of both Worlds. Factory design engineers and local knowledge. Only WEG use this formula of authorised service agents.
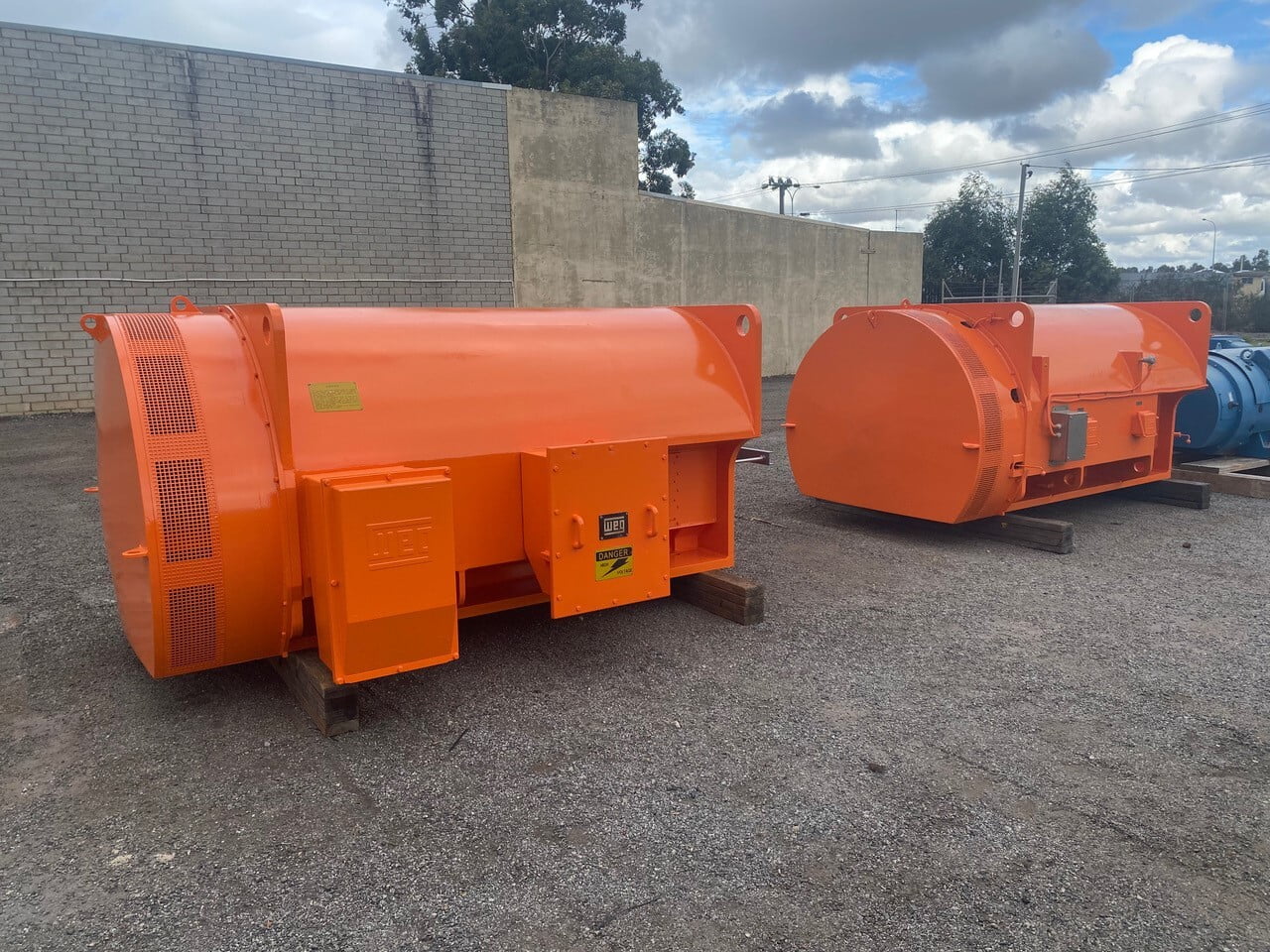